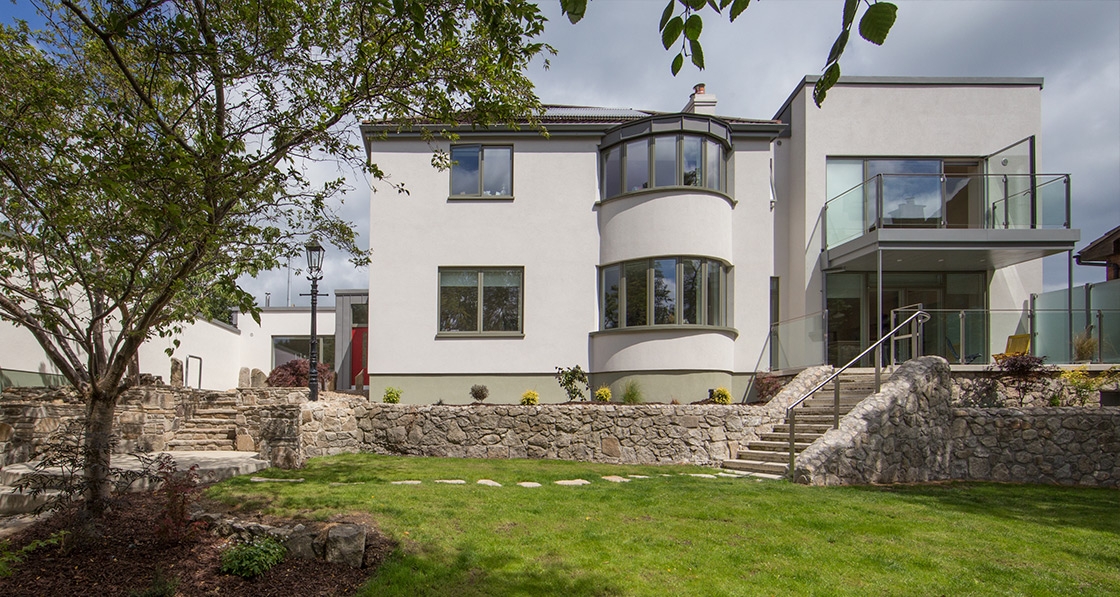
- Upgrade
- Posted
Deep retrofit transforms big, complex South Dublin home
At first glance, this sprawling house in Blackrock would appear to be a nightmare candidate for a deep energy upgrade — large and sprawling, and with a mix of structures built at different times and with different materials. But guided by the passive house standard, the team behind it managed to turn a G-rated energy guzzler into a healthy and very-low energy family home – complete with an A rating.
Click here for project specs and suppliers
This article was originally published in issue 18 of Passive House Plus magazine. Want immediate access to all back issues and exclusive extra content? Click here to subscribe for as little as €15, or click here to receive the next issue free of charge
Any builder will tell you that when it comes to refurbishment, you never really know what you’re dealing with until you start opening up the structure. Greenfield builds need careful planning and attention to detail. Retrofits need that, plus imagination and an ability to think on the hoof. A Zen-like calm would also be helpful. When architect Brendan O’Connor of Abode Design set out to extend and retrofit the Regan family’s sprawling home in Blackrock, Co. Dublin, the list of unknowns was substantial.
The house itself was 60s era, and probably of hollow block construction, while a 70s era extension on the eastern façade also seemed to be hollow block. Then there was a ‘cottage’ annex to the right, which had a stone façade and merged with an old garden wall. It was anybody’s guess what lay beneath the stone.
The house was also very big at 370 square metres, and warren-like in its layout. “The original house had charm,” says O’Connor, “but the actual flow and connection of spaces just didn’t make sense at all. You had to go up and down stairs from one bit to another, and it didn’t really make sense. It had been tinkered with over time rather than properly considered, so the brief I was given by the client was to put manners on that higgledy-piggledy nature.”
The client, Pam Regan, also had very clear ideas about the kind of retrofit she wanted for herself and her family. When asked why aim for a sustainable low-energy spec, she asked, why not? “Why wouldn’t you in this day and age? It would be silly not to. It wasn’t a big decision, it was the only way to go.” The problem however was that the house was an affront to sustainable principles. Big where it should have been small, sprawling where it should have been compact, and built with little or no insulation. It was also, she says, very cold.
This left Brendan O’Connor with twin challenges. In addition to rationalising the rambling layout and creating a bright, open space more suited to the needs of the family, he also had to transform the house into a warm, comfortable, healthy home without compromising the charm that drew the Regans to it in the first place. O’Connor chose Enerphit, the passive standard for refurbishments, as his guide. This was familiar territory for O’Connor, who was project architect for Ireland’s first – and the world’s 5th – certified Enerphit project, just around the corner at Wynberg Park, while at Joseph Little Architects (a project which featured in issue two of Passive House Plus.
“We were aiming for the most efficient construction and in my view, the principles and targets of passive house are very sound,” he says. “You don’t have to purchase expensive systems to create energy efficiency. Instead, you ensure the envelope is highly insulated and thermal bridge free, airtightness is good, and that you have a ventilation system to keep everybody healthy.”
“Those are excellent principles, no matter what building you’re working on, and those are what drove this project.”
The existing two-storey extension on the eastern elevation was judged to be substandard, and was demolished, to make way for a structure of much higher build and thermal quality. Internally, the team stripped out the existing floors and replaced them with a new concrete slab, making it possible to move freely through the ground floor without the need for steps. Internal walls were removed and the design opened up, introducing light deep into the heart of the house.
“This is a very active family,” says O’Connor.
“They anticipated that the back door to the lane would be in constant use, so I had to design the house in such a way that it worked with both front and back. That informed the new entry point with the stairs and created a nice bright focal point.”
The ‘cottage’, as it was known, was a single-storey extension on the western elevation that backed onto the lane at the rear of the house. It was stone clad, and appeared quite old. When the structure was investigated however, that turned out not to be the case.
“It was all hollow block when we opened up; it was of very strange construction. We got the impression that it was old garden walls and that someone, at some point, decided to put a roof on it.” Rather than demolish the structure, the design team decided to remodel it and place the back entrance here.
The house was wrapped with a Baumit external wall insulation system, with VM Zinc roofing and Fakro DXF triple glazed roof windows
Extensive use of external wall insulation (EWI) formed a central part of O’Connor’s refurbishment plans. Wrapping the house’s walls with a Baumit EWI system brought the U-values right down – 150mm bringing the existing walls to 0.19, with 200mm on the extension walls hitting a lower still 0.146.
It also formed a central part of the strategy on addressing thermal bridging.
“With EWI, it’s quite easy to avoid thermal bridges, because you’re wrapping the house.
Really, what you’re trying to do is make sure you meet the insulation in the roof, and that you’re near the floor insulation. You then ensure that the junction between the floor slab and the external wall insulation is of low conductivity.”
Specialist thermally broken products were also used diligently where required. Fischer Thermax fixings were used to affix rainwater systems to the EWI layer and Schöck Isokorb connectors were used where balcony and solar shade meet the external walls, in both cases keeping thermal bridging to a minimum.
Because of the thickness of the insulation, the windows sit proud of the masonry in order to avoid being lost in the reveals. Support comes from Compacfoam sole plates, a product similar to expanded polystyrene. It’s as dense and strong as timber, but its thermal conductivity is so low that the window reveals do not become thermal bridges, sucking heat out of the structure.
Internal walls were removed and the design opened up, and combined with the Fakro and Velux roof windows this introduces natural light into the heart of the house.
The bay windows on the front elevation were however a different matter. When the build team set about removing the old windows, they discovered that they were actually holding up the roof. This generated an immediate need for steel. Typically, says O’Connor, architects like to hide structural details like these in window mullions. That solution would however have introduced a major thermal bridge to the design.
Instead, O’Connor asked the engineer to specify steel with the slimmest profile possible, and then placed that steel on the warm side of envelope, just inside the mullion.
“We painted it white to match the windows,” he says, “and they appear to disappear into it. At the time however, there was a lot of debate over that. It’s one thing to say that it will disappear, it’s another thing to believe it.”
Installation of Velfac windows, while Schöck Isokorb connectors used where the balcony meets the external wall to minimise thermal bridging
The design team also sought materials that were fully breathable in order to make sure that the structure could deal effectively with moisture in the build-up.
“The minute you put on membranes and insulation, you’re either stopping heat getting to structures, which probably means condensation can happen, or you could be trapping vapour or wetness somewhere. Every time I trap something, I make sure that I’ve thought about ventilation, for the client and the structure, so both stay healthy.”
Citing the fact that masonry buildings invariably retain moisture, the external wall was finished with a breathable render. O’Connor points out that a vapour tight render could prove a real problem. “The worry then is you have moisture build up under it, and that it might de-bond over time.”
Compacfoam sole plate under EPDM membrane supporting window cill in external insulation layer, to prevent thermal bridging
Asked what his strategy was for airtightness, O’Connor says that it largely consisted of getting a good builder onsite. Tim Walsh of contractors Brian M Durkan & Co says that achieving airtightness was unquestionably the biggest challenge the build team faced.
“Because we were working between old and the new, around existing structures, the attention to detail required to achieve the target was exceptional. Certainly our foreman had less hair when he finished the job than when he started it.”
Despite the challenges that arose during the build, O’Connor says that there were no huge dramas onsite. “We had very good people. The builders were excellent, they asked questions early and gave us time to answer them. We worked together to find solutions. It’s not like there weren’t problems, but they just weren’t dramatic enough to scar my memory. The foreman, Dermot Ryan, was particularly good and I had worked with him before on another challenging low energy retrofit and knew the project was in safe hands, and if anyone could meet the arduous airtightness target he could.”
-
Site works after demolition of an earlier extension Site works after demolition of an earlier extension
-
Metal web Posi joists to intermediate floor of new extension Metal web Posi joists to intermediate floor of new extension
-
Intello membranes and airtightness detailing where the new roof meets the existing external wall Intello membranes and airtightness detailing where the new roof meets the existing external wall
-
Existing walls at lane to the read of the house, with the pebble dash wall in the middle forming of the building’s thermal envelope Existing walls at lane to the read of the house, with the pebble dash wall in the middle forming of the building’s thermal envelope
https://passivehouseplus.co.uk/magazine/upgrade/deep-retrofit-transforms-big-complex-south-dublin-home#sigProId72a601e2e0
Gavin Ó Sé of airtightness consultants and testers Greenbuild agrees: “The role of the foreman, or other airtightness champion, is crucial on a project like this. Dermot’s attention to detail and his ability to make the trades aware of airtightness throughout the build meant that the target could be achieved in spite of a very complex building.”
The central plank of the airtightness strategy was the internal wet plaster finish. Airtightness membranes and tapes were deployed liberally around ceilings, with taping at window junctions too.
“If it was a new build,” says Walsh, “you would deal with airtightness as you built, but you obviously can’t do that with existing structures.”
Walsh emphasises the importance of retaining personnel where possible, to keep continuity in terms of quality and delivery overall.
“Dermot has been with us 15 years or more, as have many of the lads who work for us. Even many of the subcontractors we work with stretch back to similar periods of time.” This means that once tradespeople have been upskilled for issues like airtightness, the knowledge is retained for future projects. For instance, Walsh points out that on the company’s standard jobs now, if a subcontractor pierces a hole in the airtight layer, it’s become ingrained practice for them to tell the foreman, with impressive results. “We’re typically hitting figures of 1 to 2 ACH on new build projects, without being asked,” he says.
In this project, the building achieved an airtightness result of 1.01 ACH – which is within the tolerance limits of the Enerphit benchmark, 1 ACH. Not that it matters. Given the size of the house, the widely dispersed footprint and the variety of materials in the structure, this is an excellent result by any measure.
It is however interesting to note that though the design and build team managed to hit this target, the house doesn’t quite make the Enerphit standard, primarily because of the ventilation solution they implemented.
Typically, a mechanical heat recovery ventilation (MVHR) system is used in passive houses to deliver cold fresh air from outside, which is warmed using heat harvested from vented stale air. The passive house standard requires air supply to reach certain temperatures before entering the living space, meaning that MVHR systems are effectively mandatory in the northern European climate. These systems are built around centralised fans and extensive ductwork. The bigger and more complex the house, the more pipes you need. In a retrofit situation, charting a course for this pipework can be challenging, to say the least.
“The amount of ductwork to supply and extract meant that it would be quite invasive in the existing house,” says Brendan O’Connor. “It was very hard to find sensible routes, so we decided to go with the demand controlled ventilation system.”
Instead of one centralised unit controlling the flow of air though the entire house, individual spaces and rooms are fitted with fans that are humidity-triggered. Less power is drawn down because the system is not running constantly (as MVHR does), but because the heat recovery element is now gone, there is a slightly higher space heating requirement.
The Regan family moved in last July, so haven’t yet had a winter to test the structure.
Pam Regan says however that she couldn’t be happier with it. “It’s gorgeous. I love it. It’s so bright and clean. I smile every morning when I get up and come downstairs."
Selected project details
Clients: Pamela & David Regan
Architect: Abode Design
Main contractor: Brian M Durkan
Civil & structural engineer: Waterman Moylan
Chartered surveyor: RCQS
Mechanical contractor: Mountain Lodge
External insulation contractor: Ecoclad
BER: OTES
Cladding supplier & roofing: A+A Quinn Roofing
Thermal breaks (sole plates): Compacfoam via Partel
Thermal breaks (balcony/solar shade connection): Schöck Isokorb via Contech
Thermal breaks (fixings to EWI): Fischer Thermax via Masonry Fixings Roof insulation: Isover
Floor insulation: Xtratherm
Airtightness products: Ecological Building Systems
Windows & doors: Velfac, via Teroco
Roof windows: Fakro via Tradecraft, Velux
Blinds: Window Fashions
Stoves: Dimplex, Scan, Stovex, via Heating Distributors
Radiators: Quinn
Ventilation (DCMEV): Aereco
Lighting: National Lighting
Posi joists: Armstrong Timber Engineering
Additional info
Building type: 370 square metre detached house from 1960. Deep retrofit with low energy two-storey side and single-storey rear/side extension
Location: Blackrock, Co Dublin
Completion date: July 2016
Budget: N/A
Enerphit certification: N/A
BER
Before: G
After: A3 BER (73.66 (kWh/m2/yr)
Space heating demand (PHPP, after): 37 kWh/m2/yr
Heat load (PHPP, after): 16 W/m2
Primary energy demand (PHPP, after): 117 kWh/m2/yr
Airtightness: 1.01 ACH at 50Pa
New ground floor: New floors – in original building and extension – constructed with 200mm Xtratherm Thin R (thermal conductivity of 0.022 W/mK) under 175mm polished concrete floor. U-value: 0.144 W/m2K
Existing walls (before): Uninsulated 215mm concrete block walls
Existing walls (after): 150mm graphite EPS (0.031 W/mK)) on 215mm solid block wall with a wet plaster finish internally. U-value: 0.191 W/m2K
Existing boundary stone wall (after): 600mm random rubble block, 40mm cavity, 120mm Isover Metac insulation between studs @400cc, a 50mm service cavity (battens @400cc) insulated with Metac, and 12.5mm plasterboard internally. U-value: 0.208 W/m2K
Existing roof (before): Sloped with mineral wool insulation. Roof tiles to sloped areas and torch on felt to flat roof areas externally. 150mm mineral wool insulation on the flat between roof joists and a combination of suspended ceiling tiles or plasterboard ceiling internally. U-value: 0.333 W/m2K
Existing roof (after): New roof constructed with 150mm Isover Ireland Acoustic Roll between rafters @400cc with additional 200mm Acoustic Roll above. U-value: 0.123 W/m2K
Extension walls: Baumit EWI system with 200mm graphite EPS (thermal conductivity of 0.031 W/mk) on 215mm solid block wall with a wet plaster finish internally. U-value: 0.146 Wm2K
Boundary wall to side extension: 215mm solid block wet plastered internally, 25mm cavity, 120mm Isover Metac insulation between studs @400cc, a 50mm Metac-insulated service cavity (battens @400cc) and 12.5mm plasterboard. U-value: 0.213 W/m2K
New monopitch roof: Zinc externally, followed underneath by 18mm marine ply, a 40mm ventilated cavity, 18mm plywood, 250mm Isover Metac insulation between rafters @400cc, a 100mm service cavity (battens @400cc) (Metac insulation to service cavity) and 12.5mm plasterboard internally. U-value: 0.118 W/m2K
WINDOWS & DOORS
Before: Double-glazed PVC windows and doors. Overall approximate U-value: 3.50 W/m2K
New triple-glazed windows: Velfac 200 triple-glazed, argon-filled, aluminium windows with low-e coatings. Overall U-value: 0.8 W/m2K
ROOF WINDOWS
Fakro DXF triple-glazed flat roof windows, including 6mm thick toughened external glass with overall U-Value of 0.88 W/m2K. Velux GGU triple-glazed roof windows with overall U-value of 1.0/m2K
HEATING SYSTEM
Before: 20 year old oil boiler & radiators throughout entire building.
After: Greenstar Cdi high-efficiency condensing gas Combi boiler and radiators throughout. Plus three (Scan, Dimplex, Stovax) room-sealed solid fuel stoves, each having no air exchange with the room and own air supply kit.
VENTILATION
Before: No ventilation system. Reliant on infiltration, chimney and opening of windows for air changes.
After: Aereco demand controlled mechanical extract ventilation system to the whole house.
Green materials: All timber furniture from PEFC certified sources, Tricoya to soffits and fascias. First fix completed for rain water harvest system which will capture rain water from most of the roof.
-
Ground floor layout and electrical Ground floor layout and electrical
-
Ground floor demolition Ground floor demolition
-
1st floor demolition 1st floor demolition
https://passivehouseplus.co.uk/magazine/upgrade/deep-retrofit-transforms-big-complex-south-dublin-home#sigProIdb65678c39e