- District Heating
- Posted
Central line
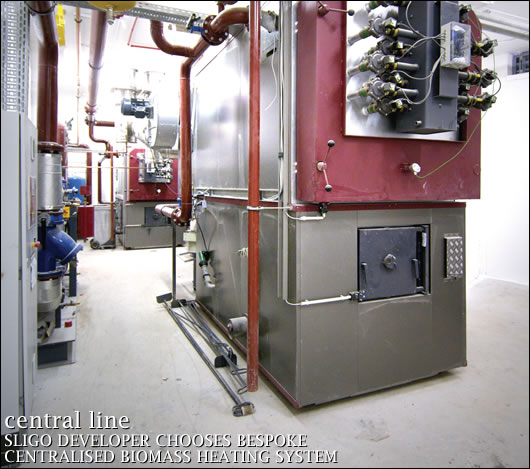
Developers across Ireland are beginning to see the sense in shifting from individual heating systems to centralised energy production feeding into district heating networks. John Hearne visited a mixed-use scheme in Ballisodare, County Sligo, where a cutting edge biomass energy centre is providing a multitude of different buildings with energy from a green, secure source.
Phases one to three of Avena Development’s residential development in Ballisodare, County Sligo, features a mix of oil and gas boilers in houses and apartments. Yet phase four, which includes a leisure centre with swimming pool, a supermarket, restaurant, ten commercial units and eighty apartments, boasts one of the largest and most sophisticated biomass district heating systems in the country.
Why such a radical change of course so late in the game? “People were very concerned with energy costs,” says Pat Gilmartin of Avena, “very concerned with the rising price of oil and gas and at the time, all the reports were that bio-fuels were at least 30% cheaper. That was the primary motivator, to do affordable living. Now we’re delivering A3 units.” Housed in a purpose built energy centre in the carpark, two Gilles biomass boilers of 550kW and 900kW take care of the entire space and water heating loads of the development. Arriving at that solution proved a long drawn out process. “There was a very, very long discussion between myself, the architects and the developers about biomass.” Derrick Healy of M&E consultants TME Services explains. “Oil was a big possibility, but no one really wanted it. It’s a dirty, expensive fuel. We also looked at storage heating, but again, this wasn’t a very popular choice. The initial concept was just to go with condensing gas boilers in each of the apartments. They’re cheap and cheerful, but Pat (Gilmartin) always had in the back of his mind that he wanted to go ‘green’. This is his second green development. He did a site in Longford that used heatpumps and solar, so basically all sorts of options were thrown around.”
Most comparable sites, when they opt for biomass, invariably combine it with a gas backup, but in Ballisodare, that convention had to go out the window. “We wrecked our heads trying to get gas in.” says Healy. “We tried to bring a high pressure gas main down along the road, but Sligo County Council said no…We hadn’t enough space on the site for tanked gas. We would have had to put in four six-tonne underground tanks, which would have taken up the whole main-square.” The topography of the site was also against them. Set in to the side of a hill overlooking the Owenmore River, groundworks were hampered by extensive deposits of black limestone. “There was a serious amount of rock-breaking.” says Healy. “We had nine months with three rock-breakers going from early morning til late at night.” Any additional excavations would have added expense and further delayed progress. “When SEI asked, ‘what’s your fossil fuel back up?’ We said, ‘no, if we’re going to do it, we’re going to do it right. Forget the fossil fuel, we’re going 100% green here.’ That’s why there are two boilers.”

The fuel store with rotary feed system suitable for woodchip or pellet
But while the site militated against gas, it was perfect for district heating. “The focus was more to try and get an urban feel or a village feel to the concept”, says architect James Griffiths of Vincent Hannon & Associates. “So it’s much tighter than a normal residential scheme. You don’t get a vast green area but you do get a high quality urban square.” The tiered arrangement of apartments set back into the hill above the commercial units, all centred on a common carpark, meant distances between heat load and heat source could be kept to a minimum. “Because the distances involved are very compact within this phase, it worked perfectly.” says Griffiths. “The other phases are more dispersed so it would have been much more difficult to get heat from a central boiler.” Moreover, because the carpark lies in that geographic centre, much of the pipework runs under its roof, precluding the need for further excavation.
Seán Gilbride of Tinteán Heating Systems in Wexford supplied the boilers. “We installed two Gilles boilers, one is a 550kW, the other is a 900kW…Initially they wanted two 700kW, but we went for the other combination because the 550kW has automatic ignition on it. More than 550kW, there’s no auto ignition, the chamber is too big, but with auto ignition, my engineer can dial into it and fire it up automatically from here.” With only the leisure centre, supermarket and some commercial units in operation thus far, only the smaller of the two boilers has been commissioned. “Come November, the 900kW will be running all the time, it will be carrying the load. If she needs back-up, she’ll get that from the 550kW, and the smaller one will cope with the load during the summer.”
Fin Engineering in Belfast, who designed and built the energy centre in which the two boilers and the fuel store are housed worked closely with Tinteán. “When we first entered this market,” says Stephen Moore of Fin, “we did our own research and decided that the Gilles boiler offered the best solution. It automatically adjusts combustion parameters up to 50% moisture content, it will also automatically regulate down to 30% of fully rated load. So say it’s a 1,000kW boiler, it will regulate down to 300kW. If the load drops below that, it will go into slumber mode. It will just keep the fire lit but under very controlled conditions. Combustion ash is less than 1% by volume of the fuel, and disposal is automatically controlled. It comes out on a little screw conveyer and there’s a galvanised steel wheelie bin that you clip into the side. The boilers are self cleaning. They have high pressure compressed air nozzles on the front of the tubes and every so often they send a short sharp blast of compressed air down the tubes to blow them clear. You don’t have to open them up every week and brush them out. They have an online diagnostics and monitoring system called FireView 2000. Tinteán look after that, but the manufacturer in Austria can also dial in and look at it too if required. When running this boiler, we’ve had to change set-point temperatures, we’ve taken the boiler down gradually and turned it off and that can all be done remotely through FireView.”
Gilles design and manufacture all components themselves, so it’s a complete proprietary system right down to the feeding augers and control systems. For maximum flexibility, the boilers can take either chips or pellets. These are stored in a purpose built fuel store adjoining the energy centre which features rotating arms and inclined augers.
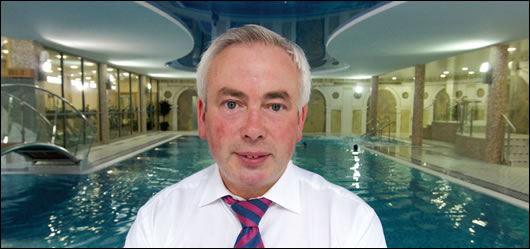
Pat Gilmartin of Avena Developments

District heating distribution pipework with insulation and Isogenopak cladding
In a high-density development, space is obviously at a premium, so how did the design team facilitate fuel deliveries? “We find the success of any biomass project is in the design.” says Seán Gilbride. Stephen Moore agrees. “These were all issues that were discussed at the time. Way back when we first met with the project manager and discussed our approach to the entire district heating solution, we talked about how long a truck would have to stand. There is a service road through the development…and the developer was happy enough for a truck to stand there while discharging. We have three fill pipes that come out in a little triangle of grass at the side of the service road and the truck stands on the service road and blows the fuel in.”
Architect James Griffiths says that this was the only feature of the energy solution that prompted any alternation in the design, and that change was not substantial. “We had to cut a bit of extra basement, but that ground was being cut out anyway so all it meant was we were extending the envelope of the basement slightly to create the holding tank for the woodchip. We also had to strengthen the roof of the holding tank to take the weight of the lorry coming in over it…The delivery point itself is very neat. All you see is three pipes with caps coming up out of the ground.” In total, the fuel store takes 40 tonnes, so there are no capacity constraints.
While the district heating solution offered a perfect fit with the development’s energy requirements, it did throw up one major potential headache. “One of the biggest difficulties was the billing arrangement for the occupants.” says Derrick Healy. “We spent this lump of money, how are we going to get it back? That’s where Tinteán really stepped up to the plate…We spoke to the controls people; ‘look, can you send out all the information to Tinteán on an Excel spreadsheet?’ They came back and said yes.”
“Our associated company, Greentree Enterprises looks after fuel supply and metered heating.” says Seán Gilbride. “So we supply the fuel to the boilers, look after their operation and maintenance, and we provide the billing service. We set up a billing engine, we bill the customers on behalf of the client, collect the money and transfer it back to the client.” With three fuel conditioning centres in Wexford, Kerry and Fermanagh, the company has sufficient geographic spread to efficiently service clients throughout the island. Stephen Moore explains that because Fin installed a bulk heat meter, Avena can avail of an energy supply contract as opposed to a fuel supply contract.
“With a fuel supply contract you’re buying so many tonnes of fuel. If it’s an energy supply contract, you just pay for the kilowatt hours consumed. It eliminates any arguments about moisture content. If you’re buying fuel you can sometimes feel aggrieved because the moisture content is high and you’re buying water.”
Tinteán estimates that compared to an oil boiler of similar size, the biomass solution should displace 827 tonnes of C02 per annum. With energy efficiency ratings of between 90% and 92%, the boilers will burn 1,250 tonnes of fuel per year to generate 3,307 MWh of heat.
Ahead of specifying the energy solution, engineer Derrick Healy modelled the development’s space heating and hot water requirements. “You design the system based on its base load.” he explains. “On the continent, you would find a very diverse mix of people living in a typical apartment development, but in Ireland, you tend to get a very similar type of person.” With apartment living still predominant among young nine-to-fivers, you have to design your system based on the usage pattern that implies. “Each apartment is getting 35kW of domestic hot water. That’s giving people a continuous draw of 13 litres per minute which would do a shower and kitchen sink quite comfortably. The average domestic heating load here is running between 7.3kW to about 9kW in the biggest apartment.” With hot water as opposed to space heating the big energy hog, Healy based the ultimate size of the boiler arrangement on a diversity rate in the apartments of 40%. In other words, the system can handle 40% of the showers running simultaneously at any one time.
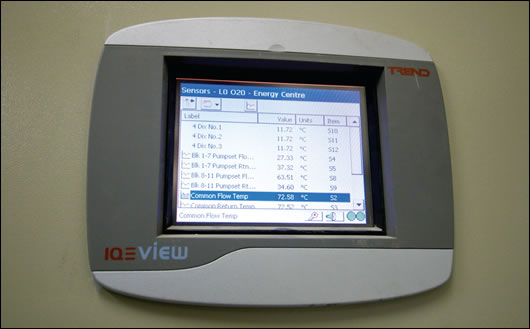
The BMS touchscreen for controlling the boilers
“The reality of this development is it’s going to hit two markets, young rental and young married couples with no kids and possibly an elderly demographic who might be trading down…When I did up the figures, I looked at the likely scenarios: what sort of usage are these apartments going to get? And the worst-case scenarios are young couples. Most work 9 to 5, so they’re all going out to work at the same time and they’re all coming back at the same time. So there are peaks, and that’s really what we’re looking at.” He concedes that this may have lead to a slightly over-designed system, but, again, given Irish usage patterns, he had to err on the side of conservatism.
“On the continent they only take a 15% diversity. Suppose you take 100 apartments and each needs 10kW. 100 by 10 is 1,000kW, or one megawatt.” Users will not however be pulling all of that down at the same time. Different types of people have different usage patterns, so, again in a European context, instead of installing a megawatt boiler, you only need 15% of that size: a 150kW installation. Similar calculations determined the heat load in the commercial units and, in particular, the leisure centre with its swimming pool. The calculations eventually determined a 1.45MW boiler combination.
During construction, Healy singles out Fin Engineering’s methodology as one of the big successes of the project. “We brought them in on a design build package for the boiler house, and no other contractor walked inside that door. Tinteán were in on commissioning, but they were in with Fin, they weren’t in for Avena. Certainly from my viewpoint, from a contractual and a smoothness point of view, that worked out extremely well. The buck stopped with Stephen Moore. If there was an electrical problem, if there was a problem with a boiler, he sorted it. “Everything was built in Belfast and brought down on the back of a truck…On site guys are about 30% efficient, because it’s raining, they’re cold, they don’t have proper light. When they’re on a factory floor, the heat is on, the radio’s on, they can work away and nine to five, and they’re working on about 70% efficiency. At one point, GMG [who installed the district heating pipework] were ready to introduce pipework to the boiler house but there was no pipework coming out of it. Fin Engineering said, ‘bring the pipe there, there, there and there.’ They gave GMG exact dimensions on a fax, GMG stopped the pipes exactly where they were told, and it worked perfectly. There was no welding. Fin Engineering brought down their pump skid and pushed it into place and bolted the pipes together. It was like Lego.”
Factory fitting lies at the heart of Fin’s approach. “Anything that could be built as a skid was built as a skid.” says Stephen Moore. “All the pumps and all of the pressurisation and expansion equipment were built as skids. The boilers were quite large so they were built in situ, but all of the pipework was prefabricated in our offsite facility in Belfast. Then we had a small team on site: two guys for two weeks, to install it and finish it off.”
He makes a compelling argument for keeping off site for as long as possible. “If you take a traditional site installation, your energy centre is the heart of your facility. Look at your Gantt chart and it’s on the critical path, because you can’t get any part of your facility handed over until your energy centre is up and running. And there are lots of sequential activities. Offsite solutions allow you to decouple all of those sequential activities into parallel activities, so we work in parallel to what’s happening on site. All our energy centre designs are modelled in 3D, and the client uses the exact same model that we manufacture from for his checking and approval. While the equipment’s on order, we’re manufacturing steel frames and pipe spools, things like that. When the equipment arrives in, it’s then assembled.” He argues that you get a better quality build offsite in ideal conditions than onsite in less than ideal conditions. “We’re not affected by weather, we don’t put in claims for extensions of time due to adverse weather. It’s a fixed cost…So what it has allowed Avena to do is ring-fence the intensive part of the facility, the heart of the facility and make somebody wholly responsible for that.”
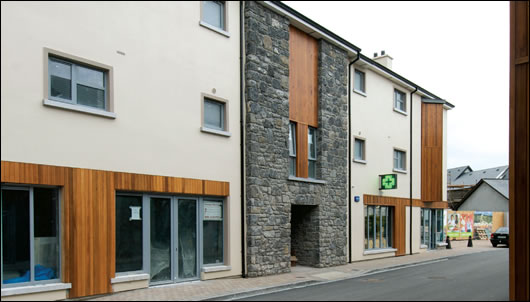
The black limestone that caused so much trouble at the early stage of the build has been extensively reused as facing material throughout the development
The energy centre serves three circuits: one to the leisure centre, another supplying blocks one to seven and the third looking after blocks eight to eleven. More than 3,000 metres of distribution pipework, along with the consumer units in the apartments, were installed by GMG Mechanical Services in Donegal. “It incorporated an advanced bracketing system,” says John Reynolds of GMG, “and the highest quality insulation/isogenapak cladding finish for the ultimate protection in the basement carpark area.”
The installation, says Derrick Healy, went like a dream. “Originally we had designed it with a view to using victaulic coupling for speed of installation, but GMG said they’d be happier to weld it. Welding was an even better job, so we accepted that.” As with Fin’s energy centre, much of the work was completed off-site, then brought to Ballisodare for installation. The Isogenapak finish was agreed upon by the design team because if a tall vehicle does hit the pipe in the carpark, it pops back out and doesn’t retain the deformity as aluminium would.
“Based on the BMS readings,” says Healy, “we’re only getting 0.5oC of a degree loss between flow and return going to and back from the leisure centre when there’s no load. It’s going out at 60oC and with everything switched off in the leisure centre, it’s coming back at 59.5oC.”
The consumer units or heat pods installed in each of the apartments have yet to be commissioned. These units, John Reynolds explains, are comprised of two heat exchangers for optimum efficiency, a built-in expansion vessel and a heat meter which can be remotely linked back to a management facility for monitoring and billing purposes. GMG also provided simple, user-friendly controls on the consumer units. “From an end-user point of view,” says Healy, “they’re no different to oil or gas systems.”
The heat itself is delivered via low water content rads in the apartments and underfloor heating in the leisure centre. The 512m2 underfloor system, supplied by Unitherm, incorporates stainless steel manifolds and Pecs piping, laid on a profile panel in order to avoid disturbing the insulation underneath. Peter Lynskey of Unitherm says that the integration of the underfloor system into the BMS has been vital to the success of the design. “It is important that underfloor is taken and incorporated into the full mechanical system so that if there’s a full BMS system going in, that the underfloor is talking to the BMS, the same way that the radiator system is and that the ventilation system is.” He says that on traditional builds, underfloor systems have sometimes been left outside the main BMS loop, leading to situations where they’re incorrectly operated and maintained
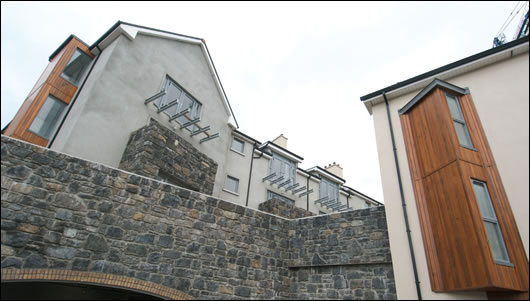
The black limestone that caused so much trouble at the early stage of the build has been extensively reused as facing material throughout the development
In the apartments, currently at second fix, the design team is aiming for an A3 rating. Insulation in the walls comes from a combination of full-fill platinum ecobead in a 100mm cavity, together with CoziBoard, the 50mm composite panel, on internal walls. This delivers a U-value of 0.19w/m2K. The figure for the roof is 0.12w/m2K, courtesy of 300mm of rockwool. The inclusion of fully 225mm of polystyrene in the floors – delivering a U-value of 0.19w/m2K – comes as a result of a design anomaly.
“The carpark structure is all in insitu concrete.” James Griffiths explains. “We have a 400mm thick slab which is a transfer slab, allowing us to build anywhere on it, independent of the column group below. That gave us a nice flat surface to the carpark which allowed us to run the pipes along the underside of the roof…but because we had a flat deck, there were no steps in it, so to achieve the difference between external and internal levels for waterproofing, we’ve built up the internal level with expanded polystyrene, so that’s your insulation and your fill to build up the floor level.”
Windows and doors, are from Munster Joinery’s Argon Gold range, and come with a U-value of 1.05w/m2K. Derrick Healy notes that in calculating U-values, the team discounted external cladding; wood, stone and metal, so that actual energy performance is better that it appears on paper. Open fires originally specified for the apartments are being blocked up and replaced with multi-fuel stoves, which have yet to be specified, while each apartment features a draft lobby.
“The other thing we looked at was heat recovery ventilation.” says Healy. “Now this was two years ago and at the time, including HRV was bringing the BER down. If I were to do it again today, you would find that the technology is after improving in leaps and bounds. The AC motor is no longer being used, they’re now using DC motors, its energy consumption is down to 2 W/L/s as opposed to 10…” The lighting spec was improved half way through the development, to incorporate extensive use of Megaman 11W GU10 fluorescent lamps in the apartments. In addition, all of the light fixtures in landlord areas and carparks incorporate both motion and light sensitivity.
Though all drinking water will come from the mains, a well bored onsite will look after the swimming pool’s extensive water needs, plus that of the laundrette occupying one of the commercial units. Rainwater harvesting was investigated but discounted. “Rock again.” says Derrick Healy. “We had nowhere to put tanks.” He estimates an eleven year paypack on the biomass boilers. “That was based on fuel prices two years ago. The way fuel prices have moved since, that’s probably come down quite a bit. Total running costs for the whole installation should be 40% to 50% of the domestic LPG price.”
Restoration of a lime-kiln onsite is at an advanced stage. Reclaimed brick and slate, along with stone found on the site have been used on the building, which, on completion will be opened as a restaurant. The black limestone that caused so much trouble at the early stage of the build has been extensively reused as facing material throughout the development. “It’s a nice touch because it’s genuine local stone.” says architect James Griffith. “You can’t get more local.” During those early stages, Pat Gilmartin brought in a grading machine and used all of that on-site material as filler, a measure which only partially mitigated the cost. “We had an awful job here.” he says. “We had e3m excavation of groundworks. It was very expensive.”
He doesn’t believe that the market has yet arrived at a point where it places a sufficient premium on energy efficiency. “I really don’t think so. You’re trying to deliver a superior product but the clients coming in don’t appreciate it, they don’t really care about A3 rated. That’s at the moment, but they will in two years time.”
Selected project details
Developer: Avena Developments
M&E consultants: TME Services
Architects: Vincent Hannon & Associates
Packaged energy centre: Fin Engineering
Biomass boiler supplier: Tinteán Heating Systems
District heating pipework: GMG Mechanical Services
Underfloor heating: Unitherm
Related items
-
The world energy crisis 2022
-
Grant heat pumps at centre of NI energy transition project
-
SEAI Energy Awards 2020 open for entries
-
The Jodrell Bank grand challenge
-
Use all your solar electricity at home rather than export it — Warik Energy
-
District heating and passive house - are they compatible?
-
Affordable passive scheme that beggars belief
-
SEAI Energy Show to take place on 6 & 7 April
-
Passive House Plus editor explains passive house to RTE's Eco Eye
-
Could the death of zero carbon help passive house bloom?
-
19th century barn gets 21st century fabric upgrade
-
Passive architect walks walk with Carlow home