- Insulation
- Posted
External examination
A growing body of evidence – including groundbreaking research published by Construct Ireland over the last year – shows that external insulation is the most effective form of wall insulation. Lenny Antonelli takes a detailed look at the energy, health and other benefits of insulating externally, while also profliling six sample projects
Everyone's familiar with cavity wall insulation, but since the launch of the Home Energy Saving scheme, another form of wall insulation has grown in popularity: external wall insulation.
Not everyone has a wall cavity to fill after all. In Dublin solid concrete was a popular choice for buildings in the 1920s, 30s & 40s, while hollow block took over from the 1950s. Looking further back, Dublin’s Georgian townhouses were built of solid brick, while old cottages scattered across the countryside were often constructed with rubble and stone. The owners of such buildings – with the exception of some protected structures – have two options when it comes to thermally upgrading their walls: insulate internally or externally.
External insulation's advantages over internal insulation are now growing increasingly clear: it offers better thermal performance and a much lower risk of condensation within the wall and on the room-facing surface of the wall. Done properly, it essentially means wrapping your house in an insulating quilt.
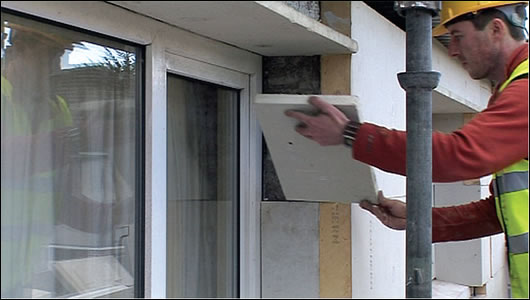
Houses externally insulated by PW Thermal Building Solutions
Energy benefits
External insulation can drastically reduce thermal bridging (the transfer of heat from the inside to the outside through junctions), something harder to achieve with internal insulation. For example, internal walls or intermediate floors typically slice through internal insulation where they meet the external envelope, creating a bridge for heat to transfer from the inside out. By wrapping the house with insulation on the outside, such awkward junctions are kept well away from external conditions.
Attention to detail when insulating externally can eliminate the trickiest thermal bridges, such as at window sills, jambs and eaves. While the technical guidance to the building regulations for refurbishment states that 15mm of normal insulation (i.e. λ-value = 0.04 W/mK) wrapped behind sills, jambs & lintels “will generally be adequate”, the reality is that this might eliminate surface condensation but will not significantly reduce heat loss.
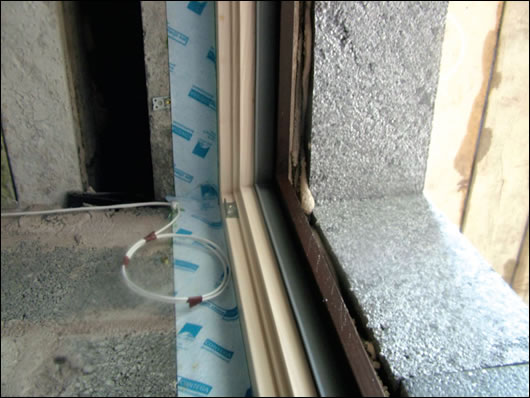
Externally insulating the sills of existing windows is particularly tricky as a host of factors – the amount of insulation, the extent of the thermal bridge, the height of the upstand to the rear of the sill, the robustness people expect of sills and their weather-tightness – are all in conflict at this point. But there are various ways skilled contractors can resolve these issues together: by cutting back the sill and insulating right up to the window, for example, or by installing a high-performance insulation around the sill and then putting a new finish over this. Insulating over reveals – typically with a thin, high-performance insulation – reduces thermal bridging around windows too.
The soffit – which connects the roof overhang with the main wall at the side of the house – is another common problem area. Because this junction is long and normally continuous, if a gap exists between wall and roof insulation here it can result in huge heat loss to the living spaces behind the wall.
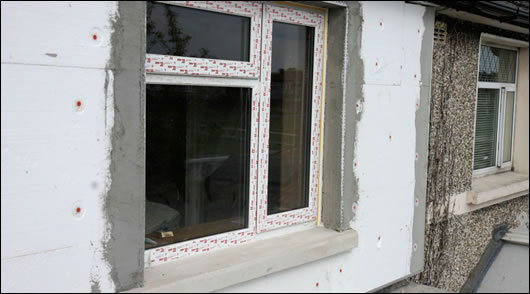
Paul Quinn of energy upgrade specialists Durkan Ecofix says thermal bridging at soffits tends to be more problematic in bungalows, where they typically meet the wall lower down, thus bringing the thermal bridge right into the living space. One solution here is to fit insulation between the soffit and the wall.
The footings of a building are another tricky spot – bringing insulation below ground level can help to reduce thermal bridging here. External insulation supplier Weber recommend using extruded polystyrene (XPS) below the damp proof course. “Because it’s a closed cell insulant it’s not negatively impacted upon by moisture,” Weber's Mark Weaver says.
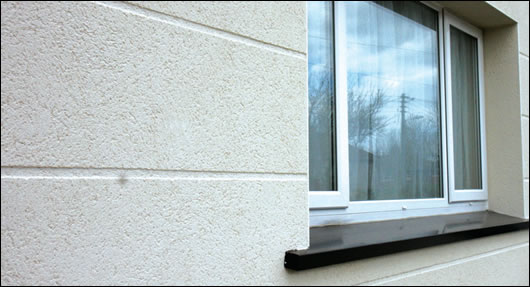
External insulation can improve a building’s airtightness too. In the second of his five-part ‘Breaking the Mould’ series of Construct Ireland articles on upgrading single leaf walls , architect Joseph Little points out that external insulation can eliminate air infiltration points such ‘hole-in-the-wall’ vents, and telecom or gas supply boxes. “A good [external insulation] system is designed to be wind-tight,” he writes. “To see a similar improvement with a drylining-focused thermal upgrade it would be necessary to examine each possible point of air ingress and apply an appropriate seal….no easy task.”
Maximising thermal mass – the ability of a building’s envelope to store heat – is typically regarded as another benefit of insulating externally. Internal insulation covers masonry walls inside and reduces their ability to store heat, but external insulation leaves the walls exposed internally and keeps them warm too, giving them more thermal mass.
Energy consultant Ciaran King of Emerald Energy published an analysis on this topic in Construct Ireland last year – his figures showed that bare and plastered concrete block walls have internal heat capacities (a more accurate term for thermal mass) of 78 kJ/m2K and 71 kJ/m2K respectively. An internally insulated wall, on the other hand, has an internal heat capacity of just 14 kJ/m2K – unsurprising given that there’s so little thermal mass on the room-side of the insulation.
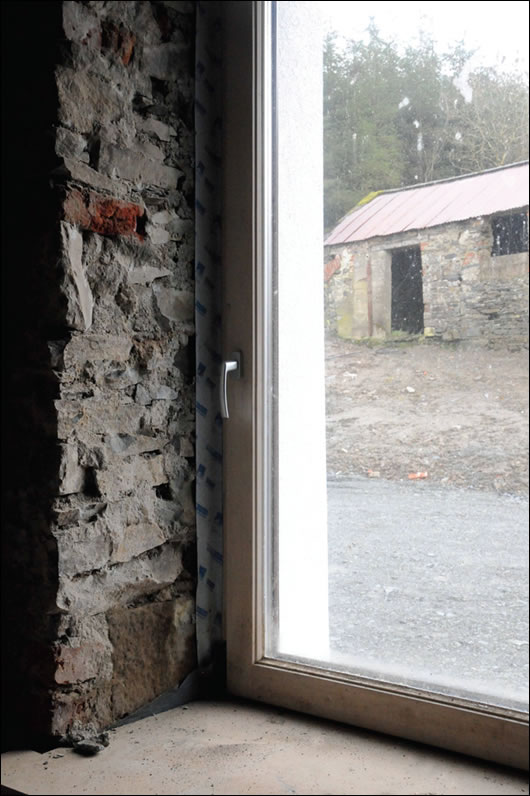
An upgrade in Cavan by architect Frank Cooney of Cooney Architects, with externally insulated exposed stone walls lending thermal mass
But King stresses that thermal mass is only beneficial in certain buildings – particularly those with a high standard of insulation, good solar gains and fairly consistent occupancy. If houses are intermittently occupied, he says heat stored in thermal mass will tend to be lost during unoccupied periods. “As insulation levels improve it tends to make thermal mass more beneficial,” he explains.
The risk of mould
Along with thermal performance, external insulation offers another big benefit over internal: lower risk of interstitial condensation. When a wall is insulated internally, the temperature of the original wall behind the new insulation falls. The temperature drop here makes it an ideal place for water vapour to condense into liquid and cause dampness, which can lead to mould and illnesses such as asthma and allergies. External insulation keeps the whole of the original wall warm and dry, minimising the risk of condensation.
External insulation manufacturer Sto performs condensation risk analysis on all its projects, the company's Barny Parks told Construct Ireland. Sto’s simulations factor in both temperature and relative humidity inside and outside the building, and the company uses weather data from Eskdlaremuir in Scotland - which holds the UK record for the most rainfall ever in a 30 minute period - in its calculations regardless of location. "It gives us a factory of safety," Parks explains.
He says Sto rarely witness a risk of interstitial condensation in externally insulated walls - if they do, they’ll typically recommend installing a vapour barrier at an appropriate point in the build-up. While Sto perform their analysis voluntarily, Parks can see such simulations becoming mandatory in future due to the speed u at which the market for external insulation is growing.
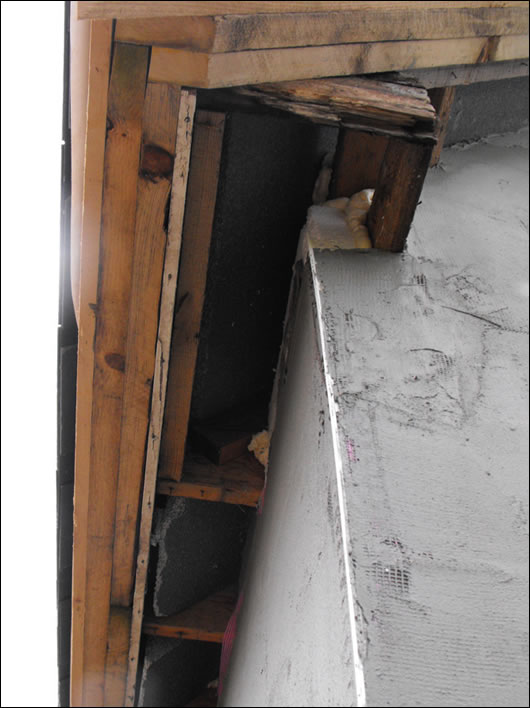
green builders MountCarrick Environmental installed external insulation between the soft and original wall of this house in Dunleer to reduce thermal bridging
In 1998, Dr Hartwig Künzel of the Fraunhofer Institute in Germany published a paper on the moisture content in different walls types – he studied a brick wall that had been internally insulated in various ways, and a similar wall with two types of external insulation. Künzel concluded that external insulation leads to the drying of the wall, with the speed of drying depending on the vapour permeability of the insulation system used. He found that internal insulation, on the other hand, causes water content in the wall to rise due to the temperature drop in the wall. “The interior insulation of exposed walls should be combined with rain protection measures at the facade,” he concluded.
No matter how well designed an internal dry-lining wall build-up is, vapour will condense inside it every winter when the temperature of the block is at its coldest. “This is because the insulation isolates the masonry wall so that its room-face cannot warm as before and consequently becomes more uniformly cool and also wetter,” Joseph Little writes. “This is typically where the most extreme temperature change takes place and vapour condenses.”
In the last of his Breaking the Mould series of articles Little published an analysis of different theoretical single-leaf masonry walls internally insulated with different build-ups. He concludes that “a troubling amount” of the simulated build-ups experience relative humidity levels above 80% – a figure commonly used to indicate likelihood of mould within a wall build-up. Some were “dramatically above” 80%.
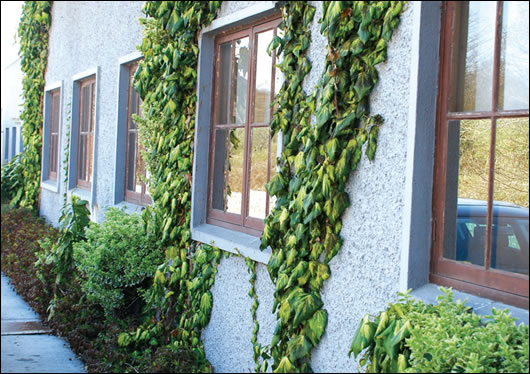
The Aerobord offices in Askeaton, Co Limerick were externally insulated with EPS in 1966. In January Aerobord removed (middle and bottom) and tested samples of the original insulation, which indicated that the thermal conductivity of the insulation is the same now as it was when first fitted.
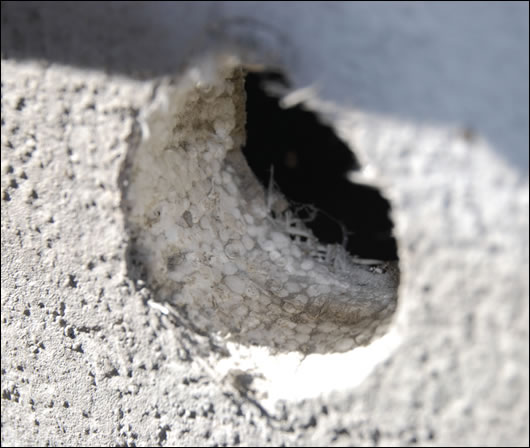
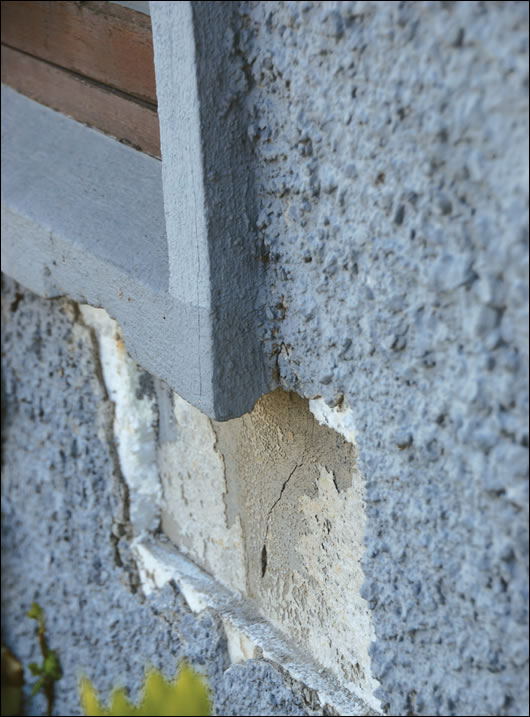
Little acknowledges some in the industry may dispute his findings based on experience – he has openly encouraged further research to expand or revise his study – but he points out that the walls of few Irish houses were internally insulated to 0.27 W/m2K before the Home Energy Saving scheme. Insulating internally to ever higher levels means less and less heat is available to the original masonry wall behind it – this in turn means that vapour moves more slowly to the outside across the old wall and interstitial condensation there has less ability to dry out. Also, mould growth behind internal insulation can develop over a long period before it becomes obvious to the householder, who could be breathing it for years before signs are visible.
Little concludes that, based on his simulations of single-leaf masonry walls, internal insulation upgrades appear to be safest and most robust when used to upgrade walls to a conservative U-value of no more than 0.45 W/m2K. In contrast his research has found that externally insulated walls appear to perform better and better when insulated to far more stringent U-values – this is because less vapour enters the warm, externally-insulated solid masonry wall, but whatever does enter can easily pass through the more vapour-permeable and increasingly cool insulation on the outside of the build-up.
As part of his research, Little also simulated a high quality brick wall insulated externally with a woodfibre system. During the simulation, relative humidity dropped from 80% to 55% – down to standard room conditions. The oscillations of this downward arc were less vigorous when the wall was insulated to 0.27 W/m2K rather than 0.45 W/m2K because the higher levels of insulation isolate the wall better from climatic extremes, making conditions in the build-up healthier and more stable.
Little summarises: “One striking conclusion of this comparative series of simulations is that higher and higher levels of external insulation appear to create healthy and ever more stable conditions within the wall build-up, while even relatively modest levels of internal insulation face tougher conditions and either fail or are bordering on failing." However, he offers a number of important caveats: principally that internal insulation can work with minimal risk of mould if the outside surface of the building is treated first to reduce the ingress of rain, and if mould-inhibiting insulation materials are used.
He says internally insulating to 0.27 W/m2K requires very careful management and, ideally, the use of specialist insulants. But he asks a pertinent question: “Is it worth all that trouble when the alternative is a good external insulation system properly applied with lower thermal bridging, less impact on the occupants, no loss of floor area, an ability to safely insulate to a higher level, and when all is said and done arguably less cost?”
What’s the cost?
His last point here is key – consumers often think internal insulation is cheaper than external, but is it really? This perception is based on straight-up comparisons of the cost of installation work, but there are other factors at play.
For a start, insulating internally means letting builders drastically overhaul the inside of a house – it can require householders to move out temporarily, to move furniture, paintings and other household items, and to re-decorate afterwards. This must be factored into cost calculation – as must the loss of floor area.
In the May 2009 issue of Construct Ireland Little articulated an idea put to him by sustainable design expert Jay Stuart of DW EcoCo and Durkan Ecofix, using the example of a typical three-bedroom semi-detached house in Dublin with hollow block walls, a floor area of 100 square metres and an external wall perimeter of 20m per floor (not including the party walls). At the time he wrote that a ‘best practice’ approach to insulating this house internally could involve using 80mm of blown cellulose insulation continuously sealed with an intelligent vapour control layer to the surrounding structure, plus a 38mm service zone filled with hemp or sheep’s wool insulation and a plasterboard finish. Such a build-up could be 130mm thick, which would result in a lost floor area of 5.2 square metres, or 56 square feet - that's €13,988 worth of floor area assuming a conservative property value of €250 per square foot. Of course Little’s more recent simulation work and writing is forcing him to look at specifying 0.27 W/m2K for internally insulating single leaf walls considering the possibility of unwanted side-effects.
It would be a mistake to respond to this loss of real estate by choosing thin and cheap materials of dubious quality that don’t allow for a proper air-tight installation or that result in poor thermal bridging, Little advises. “As with almost anything, it is better to do a little work well than a lot badly,” he says.
SEAI currently offers a grant of €4,000 to externally insulate homes. The cost of external insulation varies depending on the U-value required and the amount of work involved in a particular job – if there’s little external surface area such as mid terrace homes the grant can virtually cover the entire cost – but upgrading a typical house to a U-value of 0.27 W/m2K might cost in the region of €100 to €150 per square metre of surface wall area. However, Brian Cahill of insulation manufacturer Aerobord says prices should drop as more elements of external insulation systems arrive on site pre-prepared, lowering labour costs. “That’s what’s starting to happen in the industry,” he says.
So far we’ve focused on single-leaf walls – but what about externally insulating cavity walls? The principles are essentially the same – the key difference is how the cavity is treated. When externally insulating such a wall, in most situations the cavity should be pump-filled before the external insulation is applied.
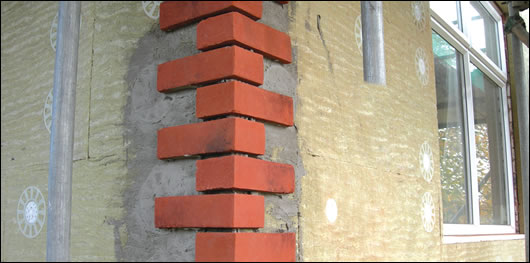
The Brickshield system from Ibstock features high density Rockwool insulation coated with an adhesive mortar and finished with Ibstock's real brick slips
What is external insulation?
Cavity wall insulation might be the best known of the long established wall insulants in Ireland, but external insulation has been around for longer than you might think. Aerobord recently tested 1.5 inch thick EPS external insulation panels that they fitted to their offices in Askeaton, Co Limerick in 1966. Though the walls were exposed to south westerly winds and driving rain, Aerobord say the thermal conductivity of the boards was the same in January of this year as they were when installed.
Some of the most common external insulation materials include expanded polystyrene (EPS), mineral wool, woodfibre-board and polyisocyanurate (PIR). External insulation can be anchored to walls using mechanical fixings (often with plastic heads, as metal conducts heat) or mortar dabs, or a combination of both. Depending on the type of external insulation used, changes to the original wall finishes – as in the case of pebble dash – are sometimes needed to ensure a smooth application.
Homeowners with single leaf hollow block walls should ensure their walls are sealed at the top before upgrading. Incidentally, the external insulation of a hollow-block wall is the only time it could be worth considering the otherwise futile practice of pump-filling such a build-up, but further research on this topic is needed.
Once the external insulation board is applied, finishes are available to create and replicate all sorts of looks, including dash and brick. Those seeking a brick finish have a number of options: renders designed to create an authentic brick effect, synthetic brick slips, or slips cut from real brick.
Indeed, one of the most exciting things about external insulation is its potential to freshen up the appearance of our drab estates. On page 71, Dermot Byrne of contractor Cosi Homes suggests that planners should start to co-ordinate the application of different colours and shades when houses are being externally insulated to do just that. Currently, external insulation is only exempted from planning permission if it “does not materially affect the external appearance of the structure so as to render the appearance inconsistent with the character of the structure or of neighbouring structures.”
Improving the appearance of our buildings is just one of external insulation’s many benefits – it won’t necessarily be the best option for every building of course, but it’s become increasingly clear that, for many homes, it’s the most effective and healthiest way to upgrade walls, reduce energy consumption and cut fuel bills.
External wool & triple-glazing at Donaghmede semi-d
Vincent Daly had good reason to upgrade his three bed semi-detached house in Donaghmede. "It was very draughty, and it couldn't retain the heat," he says.
Daly heard about the Home Energy Saving scheme and started making enquiries. With his only wall cavity sitting between the hollow block and brick facade at ground floor level, his only real option was to insulate internally or externally. He chose external, mainly to improve the look of the house and minimise disruption inside.
Home energy upgrade specialists Durkan Ecofix externally insulated the house with 120mm of Rockwool – a breathable and recyclable material – to bring the external walls to a U-value of 0.27 W/m2K. Ecofix’s Paul Quinn says the firm prefer to use Rockwool because of its breathability and fire resistance. Rockwool can also be directly applied to pebble-dashed surfaces without preparation because the wool compresses around the dash. “It’s a natural product as opposed to being an oil based product,” Quinn adds.
Weber supplied the external insulation system for the project. The insulation was fixed on mechanically with plastic-headed bolts to minimise thermal bridging. At the time of writing, the bottom half of the house was being finished externally with a Weber render and red brick finish to replicate its original look. Joints are cut down to the surface coat beneath the red finish to create a brick effect – Quinn says this produces a more authentic finish than artificial brick slips. The top half was finished with a breathable Weber acrylic render in an off-white colour.
Ecofix also pumped the 100mm cavity between the original brick and the hollow block with bonded bead from Ecobead. And to eliminate a major thermal bridge, they removed a large concrete step at the back of the house and insulated over the area where it previously joined the house.
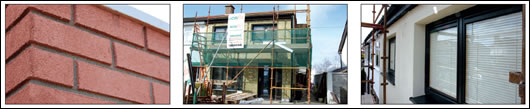
(left to right) Ecoglaze Edition 4 windows featuring a blind between the inner and middle pane; the house is externally insulated with 120mm high density Rockwool insulation; the freshly applied brick finish
Vincent Daly also installed new windows from Carlow-based Ecoglaze, who supply windows from manufacturer Internorm. Ecoglaze supplied both Edition and Edition4 windows – both are triple-glazed timber alu-clad units with argon fill, aluminum spacers and CFC-free foam insulation in the frames. The Edition units have a U-value of 0.71 W/m2K for the glazing and 0.86 W/m2K for the frames. The Edition4 units feature a blind between the inner and middle pane – they have an overall U-value of 1.0 W/m2K, but with the blinds unrolled this jumps to 0.94 W/m2K. Ecofix installed 40mm of high performance insulation around the reveals too.
Daly says his old aluminium double-glazed windows were "brutal – anytime you tried to wash them the water was seeping in." Installing new windows has eliminated draughts around the frames, he says.
Daly bought and installed bagged rolls of fibreglass in the roof himself, lagged pipes in the attic and installed a new attic hatch too. He says of his old hatch: "it was too small, the air was flying through the gaps." He has yet to upgrade his old oil boiler. "That'll be the next job I'd say,” he says.
Work was just approaching completion as Construct Ireland went to press. Though the weather was hardly freezing in April, Daly says there were still a couple of cold days that tested the house, and that it performed well. "When you come into the house it feels great," he says.
"Everyday [before the upgrade] you'd be putting on the heat just to maintain the temperature, but for the last few days you can put it on for an hour and wouldn't have to put it on after that,” he adds. “The comfort level is the main thing."
Cork semi-d with heating pipes embedded in insulation
External insulation typically just means upgrading your walls, but for one Cork family it offered them an innovative opportunity to update their heating system too. When asked to thermally upgrade a semi-detached house and heating system in Cork city with minimal disruption inside, PW Thermal Building Solutions Ltd. chose to employ a novel solution: run the pipes for the heating system, and cables for the heating controls, on the outside of the house.
D Feeney & Sons - a PW Thermal registered contractor – routed pipes on the outside face of the walls to a central manifold in the attic before applying the insulation. Gaps where services penetrated the building envelope were sealed for airtightness.
Heating and plumbing specialists Heatplan Ltd. designed and supplied the new heating system. Individual pipe circuits were routed for each radiator, meaning joints were eliminated apart from surface connections at the manifold and radiators. Interestingly, thermal imaging detected only a 1C difference between parts of the outside surface with piping underneath and the rest of the wall.
The original walls were treated on the outside to prevent mould growth, while down pipes were altered to allow for the new thickness of external insulation. 100mm of Powerwall polyisocyanurate (PIR) board was fitted externally to the walls, boosting their U-value to 0.20 W/m2K. Grooves were cut in the back of the PIR board so it could fit snuggly around the insulated 16mm piping. The insulation was finished with an adhesive coat into which an alkali resistant mesh was embedded, followed by a second adhesive coat and then a wet dash finish to replicate the house's original look. 60mm of extruded polystyrene (XPS) was installed externally below the damp proof course.
Powder-coated aluminum sills were fitted over existing concrete sills, and three layers of polyurethane were placed between the old and new sills to help prevent thermal bridging. With the clients keen to maintain the original look of the house, PW Thermal installed Isoklinker insulation brick panels – which come pre-fitted with brick slips – to replace original brick detailing around the door.
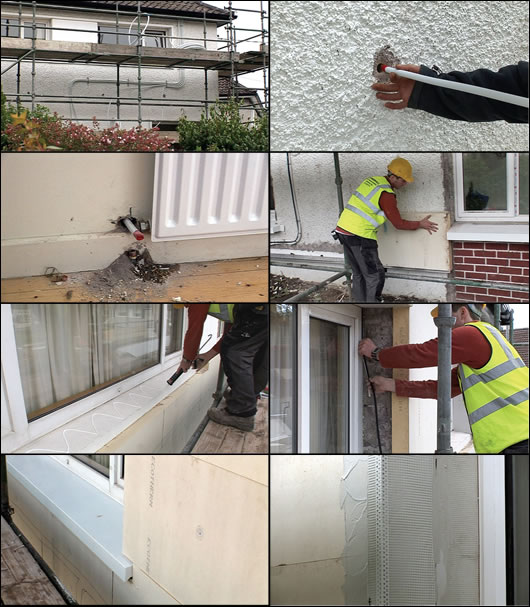
(top to bottom) Hugh Egan’s home is upgraded with joint-free heating pipes attached to the external walls and fed through the walls; insulation applied to the wall; the window sill is prepared for polyurethane insulation and a powder coated aluminium over-sill; sealing around the window before insulating the cutback reveals; insulation is cut and fitted around the new sill; an adhesive coat with embedded alkali resistant mesh is applied
Homeowner Hugh Egan opted to keep his original double-glazed PVC windows, and the contractor removed the existing plaster reveals around windows and installed 30mm of PIR board here. All window and door reveals were insulated to minimize the effect of thermal bridging in accordance with the Acceptable Construction Details document published by the Department of the Environment, achieving an R-value of 0.6 m2k/W.
Originally built of hollow block in the 1950s, with dry lining subsequently installed to first floor rooms showing clear evidence of mould growth, the house was poorly insulated with a dated heating system that lacked any proper zonings or control over air and water temperature. Mechanical contractors for D Feeney & Sons installed a new high efficiency condensing gas boiler, with the heating system designed by Heatplan divided into three main time zones – upstairs, downstairs and hot water – with electrical thermostats in every room. The option remains to install programmable room thermostats, or to upgrade to any type of controls that may be developed in the future because of the way the system was installed with individual pipe and cable runs.
The house now features solar thermal panels too, and the upgrade boosted its Building Energy Rating from an E1 to a B3. “The freezing weather earlier this year has now encouraged more homeowners to think about insulating,” says Kieran Carew of PW Thermal Building Solutions.
Homeowner Hugh Egan says that the upgrade has made a “huge” difference inside the house, which was finished in December. “The house remains warm even after a cold night with no heating on since 9pm the previous night,” he says. “It seems to be doing a fantastic job.”
Two house facelift in Beaumont, Dublin
There's little doubt now that external insulation works when it comes to thermal performance, says Dermot Byrne of contractors Cosi Homes - the question is how much can be achieved with it. Speaking to Construct Ireland, Byrne is keen to emphasise the potential for external insulation to breath new life into our tired old estates.
"I think we're passed the stage of whether it works, everyone is convinced now that it does work," he says, adding: "When you are upgrading dull and dreary roads, you could have them looking very fresh and very nice."
Byrne would like to see the planners get involved, and start to support and co-ordinate the application of external insulation to improve the appearance of our streets. There's great potential for planning officials to co-ordinate the application of different shades, colours and tones to houses on a street to improve the overall look, he says.
Cosi Homes install Parexlanko Parisio Mince external insulation systems, and the company recently finished upgrading two semi-detached houses in Beaumont on the northside of Dublin city. Byrne says the mineral render with the Parisio Mince system can achieve a greater variety of finishes than acrylic renders. "It's more natural and it blends with what's there," he says. “The breathability is better on it than acrylic.”
The two uninsulated single-leaf hollow block 1950s Beaumont houses were upgraded within two months of each other after word spread among neighbours – the first was insulated externally with 120mm of high density aged EPS, the second with 120mm of Rockwool. Once the insulation is fitted, Cosi Homes apply an undercoat with an embedded mesh and another layer of undercoat, followed by the mineral render.
The company also installed 300mm of fibreglass in the attic of the second house along with a new condensing gas boiler delivering to three heating zones: upstairs, downstairs and hot water.
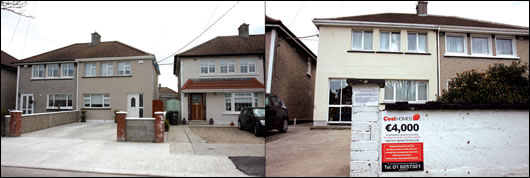
Such is the contrast between the newly insulated and rendered house, it’s little wonder that Cosi Homes were soon able to encourage a neighbour on the road to follow suit; and effective on-site advertising may encourage other neighbours and passers-by
The upgrade boosted the building energy rating of the house from 307 kWh/m2/yr to 169 kWh/m2/yr – from an E1 to a C1 in other words. This reduced the calculated carbon emissions from 58 kg/m2/yr to 32 kg/m2/yr. Based on SEAI’s standard measurements (which don’t take user behaviour into account), this should reduce annual costs for heating, hot water and lighting from €1,900 to just over €1,000 – quite a drop.
Cosi Homes has recently developed new thermal bridging prevention details for tricky spots like sills, jambs, and eaves – these details include installing 50mm of phenolic insulation between soffits and the main wall to ensure continuity of insulation, placing strips of high performance insulation over the original concrete and under an aluminium finish at sills, and installing strips of similar insulation at jambs.
Architect-designed Kerry bungalow upgrade
The upgrade of a new bungalow in Kerry demonstrates the potential of external insulation systems to transform the appearance of tired buildings. In a stunning location overlooking Kenmare Bay, the house was transformed from a dated bungalow to a strikingly modern home.
The house’s 75mm wall cavity, already partially filled with polystyrene board, was first pump-filled with platinum polystyrene bead. The walls – which originally had a shallow dash finish – were then externally insulated by Greenspan using the Brillux external insulation system. "Brillux is based on either polystyrene or mineral wool," says Greenspan's Chris Scanlon, "in this particular case we used EPS [expanded polystyrene]." The Brillux system is treated to prevent algae from growing. "It's a standard part of the system," Scanlon says.
The insulation was both adhesively and mechanically fixed to the walls, which Scanlon says should help the durability of the system in its exposed location. Greenspan used 60mm of platinum EPS – Scanlon explains that platinum EPS makes a better insulant than typical white EPS, but that it’s a little more expensive. The upgrades will bring the U-values of the external walls to 0.22 W/m2K.
Outside the insulation, the Brillux system is completed with a base coat with fiberglass mesh, a primer and a white acrylic finish. The windows were brought forward to sit in line with the outer layer of insulation, so there are essentially no reveals. The windows are full height, meaning there are no sills to deal with either. Greenspan installed EPDM seals behind the insulation around windows and doors to prevent air and moisture leakages.
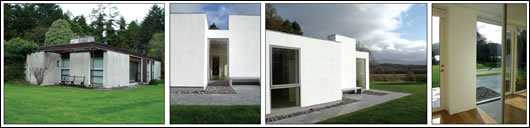
(left to right) Windox supplied the double glazed windows, which have an overall U-value of 1.1W/2K; the house sits in a stunning location overlooking Kenmare bay; the re-design by Carson & Crushell has drastically updated the appearance of the dated bungalow
A small section of wall with timber cladding outside was the only part not to be externally insulated. Greenspan installed 50mm of high density EPS 200 from the plinth line down to the foundations, with a waterproof base-coat on this. "It's a standard detail we have when we go below the plinth," Scanlon says.
Inside, the house was completely gutted – the interior was totally remodelled, with two small bedrooms converted into one large en-suite, turning the four bedroom house into a three bedroom one. The homeowners had originally intended to extend the house, but project architects Carson and Crushell talked them out of it, encouraging them to make better use of existing space instead. Outside, a new limestone terrace outside overlooks Kenmare Bay.
New double glazed windows with a U-value of 1.1 W/m2K were installed by Windox. Ten inches of Knauf Frametherm mineral wool insulation was laid in the attic, and 20 evacuated solar thermal tubes from Absol installed on the roof. A new Firebird Heating Solutions condensing oil boiler now heats the house, which was also rewired electrically with low energy light fittings throughout. The upgrade – overseen by Jeremy Walsh Project Management – boosted the BER of the house from an F to a B3.
Whole envelope upgrade to Crumlin hollow block house
A typical semi-detached hollow block house in Crumlin is now starting to feel the benefits of external insulation thanks to a new upgrade. Home Upgrade Solutions (HUS) – the renovation arm of contractor Cunnane & Donaghey – was in the process of externally insulating the house with EPS as Construct Ireland was going to press.
HUS insulated the house with a Weber external insulation system – it features 120mm of EPS with a lightweight adhesive coat outside this, and is finished with an acrylic render, which features an aggregate to add texture. "The two products just stick to each other," says Weber's Mark Weaver. "The base coat sticks to the insulation and then the render sticks to the base coat."
HUS fixed the insulation to the house using mushroom-headed bolts with plastic heads to reduce thermal bridging. The upgraded external walls now have a U-value of 0.27 W/m2K.
HUS's James Whyte emphasises that external insulation and the new white finish will freshen up the house's appearance. "It'll make it stand out considerably," he says.
HUS insulated with 50mm of Weber's extruded polystyrene (XPS) below damp proof course. According to Mark Weaver, XPS rather than EPS is used here because it's a closed-cell insulant, so is "not negatively impacted upon by moisture,” he says.
Weaver emphasises the importance of seeing external insulation as a whole system, rather than a set of individual components. "The reason it's critical all the products are applied together is because any third party accreditation [such as NSAI Agrément] is based on all the components being tested together," he says, adding that Weber can use three or four different insulation types as part of their systems, but only sell whole systems. "The crucial thing is all the components working alongside each other to make a system perform.”
HUS insulated the attic with 300mm of Knauf Ecose insulation, while a 15 square metre flat-roof extension was insulated with 150mm of Ecose and 60mm of Xtratherm board. Knauf Ecose is a glass mineral wool insulation produced with up to 60% recycled glass and using Ecose binders, which are free from formaldehyde, phenol and acrylics, as well as artificial colours, bleaches and dyes. The binder's embodied energy is 70% less than a conventional equivalent, Knauf say.
Homeowner Mick Hyland had installed new double-glazed windows before HUS arrived on site and due to an unusual original design feature, his costs were reduced to the tune of at least one window: “Most of the houses in the estate only have one street-facing window on the top floor,” says Whyte. The windows were brought forward to sit in line with the wall – when the external insulation was installed, it formed the new reveals itself and thus reduced thermal bridging here. Hyland also installed a new high efficiency gas boiler.
"It made sense to change the house from being 100% inefficient to being 100% efficient," Hyland says. Of his decision to upgrade the walls, he points out that householders can install double glazing and attic insulation but that there's "no point buying a jacket and not buying a hat." He chose external insulation as he didn't want to lose space inside, particularly as insulating internally would have meant narrowing his staircase. "The fact is that when you have it done on the outside it gives you a brand new house," he says, “it just seems like the logical thing to do.” He adds that the €4,000 SEAI grant for external insulation was appealing too.
Home Upgrade Solutions provide a range of home upgrade services, and has the exclusive Irish residential market agency for world-renowned Swedish solar thermal panel manufacturer S Solar.
Sandyford system goes up brick slip by brick slip
One of the main challenges with applying external insulation can be replicating the look of buildings with old brick facades – how to replicate the aged, weather-beaten brick look? Some clients prefer new-looking acrylic brick finishes that won't lose their sheen, others want a more traditional look.
External insulation contractor Homeglo recently upgraded a detached house on the Sandyford Road in south Dublin. The company specified cut brick slips – essentially a slice of a real brick – to replicate some of the original detailing on the ground floor. "To do it properly you have to replicate the front. It's more authentic looking because it's actual brick," says Homeglo's Frank Holt. "If you're passing by it you wouldn't notice the difference."
The single-leaf hollow block house was built in the 1950s. Holt says the possibility of externally insulating and finishing with a real brick slip is creating serious interest among architects and homeowners. Dublin is full of uninsulated brick houses, and Holt expects the demand for external insulation with real brick finishes to surge.
Homeglo insulated the house with the Baumit external insulation system, which is supplied in Ireland by CPI Ltd. The system typically includes 120mm of EPS insulation – although the Baumit NSAI Agrément cert also includes mineral wool – which is fixed to the wall with a highly polymerised cementitious dry mortar. Outside this is a reinforcing mesh in two layers of mortar base coat, followed by the primer and an acrylic render. Homeglo's Frank Holt says you "never have to paint your house again" with such a system – just power-hose it.
As Construct Ireland went to print, the company was starting to externally insulate another detached house in Terenure in which the client was keen to retain the original red brick and pebble dash frontage. Holt says the house features awkward brick detailing that will test the ability of real brick slips to exactly replicate the original look.
At Sandyford Road, Homeglo insulated all four sides of the detached house, bringing the U-value of the external walls down to 0.27 W/m2K. Homeglo specialise in external wall insulation, but Holt says he wants to carefully add other services to his repertoire, such as insulating attics and the roofs of garages.
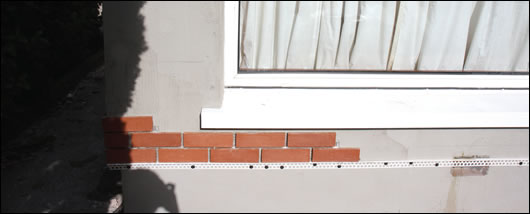
The brick slip finish by Homeglo being applied to the newly insulated walls on the ground floor
Homeowner Liam Hyland says he considered internal insulation but opted against it after considering the disadvantages – loss of floor space inside for one, the trouble of redecorating after, and the fact that external insulation eliminates thermal bridging much more effectively than internal. "When you go external there is no limit on it to be honest," he says.
The upgrade will maintain the original look of the house, while freshening it up too. The brick was just being applied as Construct Ireland was going to print: "I think it gives it a very nice finish from what I've seen of it," Hyland says. "Your house probably looks substantiality better [than before]."
- Articles
- insulation
- External examination
- External Insulation
- cavity insulation
- thermal performance
- thermal mass
- platinum polystyrene bead
- Brillux
- knauf
Related items
-
Ireland’s first 3D printed homes insulated with clay foam
-
Unilin Ireland launches embodied carbon report
-
It's a lovely house to live in now
-
Ecological launches Retro EcoWall for internal wall insulation
-
Xtratherm name changes to Unilin
-
Ecological Building Systems launch Retro EcoWall for internal wall insulation
-
Kore launches low carbon EPS
-
Kilsaran gets NSAI cert for EWI to steel frame
-
Steico offering free wood fibre insulation samples
-
Top 5 questions about specifying structural thermal breaks
-
Major new grants for retrofit & insulation announced
-
How will we decarbonise heating?