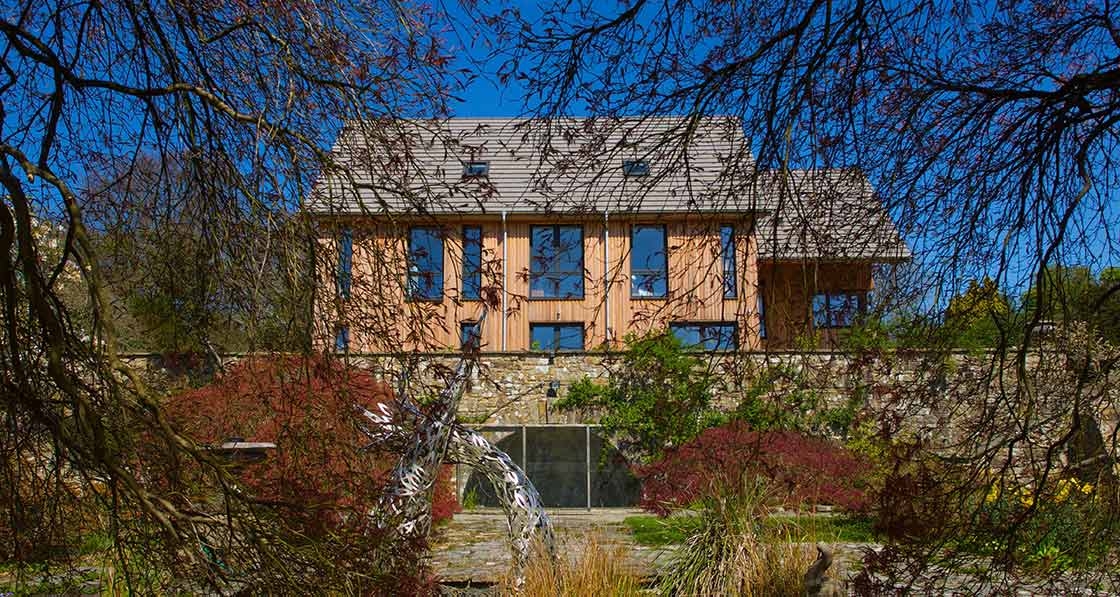
- Feature
- Posted
Larch-clad passive house inspired by a venn diagram.
With an intricate design based on the concept of two pitched-roof sections that overlap, this eye-catching timberframed Sussex home proves you can meet the passive house standard with just about any shape.
Click here for project specs and suppliers
£317 annual estimated heating costs.
Building type: Three-storey, 420 sqm timber frame house
Completed: June 2015
Location: Mayfield, East Sussex
Build method: Timber frame
EPC: B
Standard: Certified passive house
Budget: £900,000
In designing a passive house for a private client in Mayfield, East Sussex, architect James Galpin of Hazle McCormack Young LLP was asked to create a home that felt “at one with the gardens in the surrounding landscape, but which also performed well thermally”.
The brief was particularly challenging as Galpin was given a strict budget for a large house that had to accommodate a family with five children.
The central design involved overlapping a pair of traditional pitched roof house forms to create a three-dimensional ‘Venn diagram’. This overlap created the heart of the house — the entrance atrium and staircase.
Each of the rooms surrounding the central atrium has direct views along the principal axis lines of the surrounding landscape, as well as from room to room, creating an interior which “feels like a sheltered part of the garden,” Galpin says.
He continues: “The key characteristic of this site is the mid-century Percy Cane [a renowned English garden designer] landscape design and its rural setting. Our intention was to create strong visual links between the interiors and the landscape from each of the principal rooms.”
Although the Venn diagram design facilitated connection with the landscape, it reduced the efficiency of the surface area to volume ratio, creating more surface area through which heat could escape, making it trickier to reach the passive house standard.
Galpin’s team managed to overcome this problem by insulating both the walls and roof to onerous U-values of around 0.09, and a similarly impressive 0.105 in the ground floor thanks to the Isoquick insulated raft foundation system. The measured primary energy demand is almost exactly as modelled in PHPP, the passive house design software, at 95kWh/m2/yr. The owners report that it is warm and comfortable inside, even when they return from a period away.
Architect's comment
The original house on the site was a 1950s bungalow with space in the roof. It was very poor in terms of thermal performance, being very cold in the winter and using a large amount of oil to heat. The initial brief for the replacement dwelling was to create a house which felt at one with the surrounding landscape, which enjoyed the views of the gardens and performed well thermally.
Our intent was to create strong visual links between the interiors and the landscape from each of the principal rooms, plus interconnecting views, which follow the landscape axis, between the interiors of the house.
In order to maximise these views the floor plan was staggered along the central three-storey atrium space. This worked well for the layout and the connection with the landscape, but served to reduce the efficiency of the surface area to volume ratio.
A pair of traditional pitched roof house forms were overlapped, creating a three dimensional Venn diagram, where the overlap is the central heart of the house: the entrance atrium and stair. This overlap is expressed externally with a full dimension roof light, which serves to bring warmth into the house in the wintertime.
The entrance to the house supported a closing of the interior to the west elevation, which helped with summertime overheating, but views to the east of the site were crucial to the enjoyment of the interior spaces, so a careful balance of the shading had to be calculated.
We also developed a wire structure to hang from the overhanging eaves which would support deciduous vine growth to prevent solar overheating in the summer, but would die back to allow welcome solar gain in the winter months. The ventilation design was carefully tweaked using PHPP with window opening sizes amended during the design process.
The result was a reduction in summer overheating that meant the vine suspension system did not need to be fitted.
The client also says heating bills are around £2,000 less per annum than the 260 sqm bungalow that used to be on the site, though the house is not occupied full-time, making exact comparisons tricky. The large MVHR system allows the dwelling to cope with variations in the number of inhabitants (the house can have as many as 22 occupants when guests are over).
Throughout the project, the technical challenges were compounded by the requirement to stick within a strict budget of £900,000. While this might seem like a hefty figure, it had to include a two-storey guest house / garage building as well as the main passive-certified dwelling.
Budget issues were discussed at every meeting and the contractor, architect and client all searched across suppliers for the best deals on fittings, furnishings, sanitaryware and other components. “The challenge was met well, with a high-performing building built from top quality materials for less than £1,800 per square metre,” says Galpin.
Explained
Heat loss form factor is a measure of how compact a building is. It is the ratio of the surface area of the thermal envelope to the treated floor area. The higher the figure, the less compact the building, meaning there is more surface area from which heat can escape, making it more difficult to meet the passive house standard.
Contractor Richardson & Peat prefabricated the timber frame system off site, and it features 400mm studs insulated with Knauf Frametherm mineral wool. At an early stage, a decision was taken to use Siberian Larch cladding which, once it has weathered a bit, should fit in nicely with the surrounding limestone terraces.
But before construction could even begin there was a delay caused by high winds endangering the safety of the workers. The site is quite exposed at the top of a valley, where south-westerly prevailing winds sweep through, and the OSB boarding to the face of the timber frame panels acted like sails in strong winds.
“It forced the erection process to halt several times due to health and safety issues, but we managed to recover the programme time after the initial delay,” Galpin says.
This article was originally published in issue 22 of Passive House Plus magazine. Want immediate access to all back issues and exclusive extra content? Click here to subscribe for as little as €10, or click here to receive the next issue free of charge
While the original kitchen design featured a bi-folding door that met at one corner of the house, opening that whole corner to the garden, in reality there was no product on the market at the time which delivered the required level of airtightness.
“Despite these minor glitches, the house was erected without any major problems due to the accuracy of the IsoQuick raft insulation and the timber frame panels,” Galpin says.
He concludes: “The client enjoys modern architecture and is happy with the way the house sits comfortably in its rural setting, but feels contemporary in its design. It’s also the first house interior they have experienced where the temperature is stable, continuous and comfortable, without draughts and cold spots.”
Selected project details
Architect: Hazle McCormack Young LLP
Passive house consultant: Aaben Ltd
Structural engineering: Crouch Waterfall Ltd
Main contractor & timber frame: Richardson & Peat
Passive house certification: Warm
Mechanical contractor: Thomson Ellis Ltd
Electrical contractor: Ambassador Electrical Services Ltd
Airtightness testing: Anglia Air Testing
Mineral wool insulation: Knauf
Insulation foundation system: Isoquick
Window & doors: Norrsken High Performance Windows & Doors
Roof window: Glazing Vision
Pressed metal radiators: Myson
MVHR: Systemair
Lighting: Collinwood Lighting
In detail
Building type: 420 sqm detached three-storey timber frame house, plus additional 110 sqm two-storey building w/ garage & housekeeper’s annexe.
Location: Mayfield, East Sussex
Completion date: June 2015
Budget: £900,000
Passive house certification: Certified Energy bill: £317 per year for space heating, not including hot water (calculated using space heating demand from PHPP and average cost of home heating oil and wood logs as published by www.confusedaboutenergy.co.uk).
Space heating demand (PHPP): 15 kWh/m2/yr
Heat load (PHPP): 11 W/m2
Primary energy demand (PHPP): 95 kWh/m2/yr
Airtightness (at 50 Pascals): 0.5 ACH
Energy performance certificate (EPC): B (86)
Heat loss form factor (PHPP): 2.47
Overheating (PHPP): 9.8%
Thermal bridging: Use of IsoQuick floor raft to enable thermal bridge free ground junction. IBO accredited details for panellised timber frame construction.
Ground floor: 250mm concrete slab on 350mm IsoQuick PHI-certified insulated foundation system. U-value: 0.105 W/m2K
Walls: Factory-built timber frame with 22mm larch cladding externally, followed inside by 50x50mm treated battens, Protect TF200 windproof facade membrane, 9mm OSB board, 400mm Knauf Frametherm-filled I-joist timber stud, 15mm taped and sealed OSB-3, 50mm service cavity insulated with Knauf Frametherm insulation, and 12.5mm BG Gyproc Wallboard internally. U-value: 0.0.87 W/m2K
Roof: Fibre cement slates externally on 50x35 battens/counter battens, followed underneath by Protect TF200 breathable membrane, 400mm timber I-joists fully filled with Knauf Frametherm, 15mm taped & sealed Medite Smartply OSB-3, 50mm service cavity insulated with 50mm Celotex, 12.5mm plasterboard ceiling. U-value: 0.082 W/m2K
Windows: Norrsken Passiv+ triple glazed aluminium-clad timber windows, with argon filling and an overall U-value of 0.86 W/m2K Roof window: Glazing Vision fixed triple glazed Flushglaze rooflight with solar control glass & Ritec easy clean coating. Overall U-value: 1.0 W/m2K
Heating system: Grant Riello RDB 15-26kw oil fired condensing boiler serving 4 radiators and 6 towel radiators. 4kW Morso S11 90 wood burning stove.
Ventilation: Systemair SAV E VTC 700 Full MVHR. Passive House Institute certified heat recovery rate of 77%.
Green materials: All timber furniture from PEFC certified sources, material from demolition of existing house re-used in landscaping ground works.
Image gallery
-
1592_108_C4 1592_108_C4
-
1592_110_C2 1592_110_C2
-
1592_111_C3 1592_111_C3
-
1592_120_C1 1592_120_C1
-
1592_125_C1 1592_125_C1
-
1592_128_C1 1592_128_C1
-
1592_131_C1 1592_131_C1
-
1592_142_C5 1592_142_C5
-
1592_150_C1 1592_150_C1
-
1592_151_C1 1592_151_C1
-
1592_152_C1 1592_152_C1
-
LS_ELE_00_colour LS_ELE_00_colour
https://passivehouseplus.co.uk/magazine/feature/larch-clad-passive-house-inspired-by-a-venn-diagram#sigProId7f7f7b3ba6