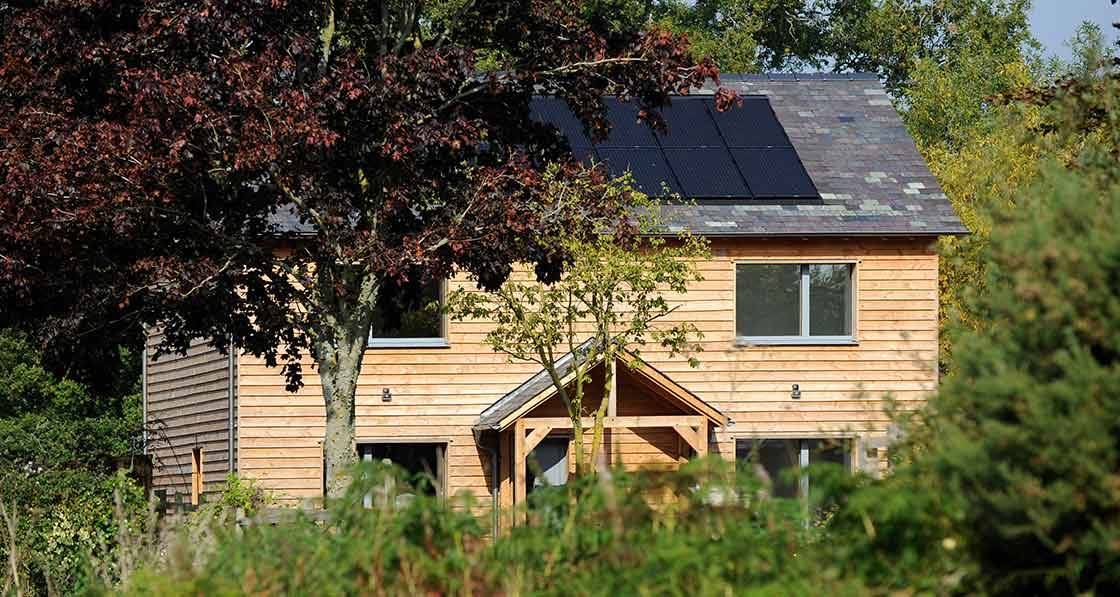
- New build
- Posted
The West Midlands eco house with no energy bills
With low electricity and gas bills and a feed-in tariff from its solar photovoltaic array, this simple, ecological timber frame passive house near the Welsh border manages to make about a £50 profit on annual energy costs.
Click here for project specs and suppliers
Building type: 140 sqm detached two-storey timber frame house Completed: May 2015 Location: Garway, Herefordshire Budget: £276,000 in total (£1,431 per sqm for finished house) EPC: C79 Standard: Uncertified passive house -£50 per annum
£730 feed-in tariff for solar energy minus £680 bill for electricity & gas
Although they loved their beautiful 18th century cottage in the Herefordshire village of Garway, Dave Atkinson and his wife Claire reached a point three years ago when they were fed up with the draughts blowing through, and with the “bottomless pit” of money they spent on heating.
They decided to build a new timber house in the garden and sell the old cottage. At this stage, they had no intention to build a passive house, but a visit to a passive house in the nearby village of Clehonger changed their minds.
“I was immediately hooked on passive house. The ambience felt just right,” says Dave.
He approached Charles Grylls of Dempsey Decourcy Architects, who then teamed up with contractor Mike Whitfield — who had worked on the Clehonger house — and the experienced passive house consultant Nick Grant.
From the outset, the team had to operate under certain restrictions.
First, Dave and Claire Atkinson’s budget was tight, although one advantage was that the couple already owned the land.
But ultimately the team managed to stick to his budget, and the completed 140 square metre ‘Ty Pren’ (meaning ‘timber house’ in Welsh) ended up costing £276,000 in total, a figure that included landscaping, a double garage and a workshop.
This article was originally published in issue 23 of Passive House Plus magazine. Want immediate access to all back issues and exclusive extra content? Click here to subscribe for as little as €15, or click here to receive the next issue free of charge
But there were also stylistic restrictions on the design. Local planning officers insisted that it had to be built in a ‘ cottagey’ style to match the existing dwellings on the edge of Garway Common.
“It had to be modest and simple, but this worked well with maintaining a continuous thermal and airtight envelope, which is so important in passive house design,” said Charles Grylls.
The airtightness test gave a result of 0.16 air changes per hour, one of the best ever recorded in the UK. The team also pioneered a way of designing the building that helped to eliminate thermal bridging at the wall-to-floor junction.
“Normally, the timber frame I-beams rest on the slab, or foundation, whereas we have perched the standard frames on the edge of the slab. Though it looks precarious, we worked closely with the engineer to maintain its integrity. We’ve done tests and it’s fine,” said Nick Grant.
“When it’s all finished it’s incredibly strong. As far as I know we were the first to do passive houses in this way, but others have since copied the method.” This is part of an approach that Nick Grant calls “ radical simplicity in passive house timber building” — fundamentally, it’s all about simplifying construction details and designing them in from the start, so that achieving airtight and thermal bridge free construction is easier, faster and less costly.
For many architects, the term ‘value engineering’ has negative connotations of contractors substituting in cheaper materials and details, potentially undermining their design intent. Grant believes the term needs rescuing — genuine value engineering, he says, is really about designing simple, effective and repeatable details.
“It’s about optimising design and performance, it’s about not using more materials than you need to. And there’s an elegance and deep beauty in that,” he says.
“Value engineering is usually misconstrued as cost-cutting, but really it should be about making things as efficient as possible, making them easier to build, and saving money and time. With real value engineering, the value increases if the cost comes down without sacrificing performance.”
“There’s no loss of performance, in fact there’s improved performance. If sustainable building is to make any difference at all, it must work really well and be affordable.”
Ty Pren was completed in May 2015, so Dave and Claire Atkinson have had more than two years to assess its energy performance. Dave says the house requires only five large bottles of propane gas per year to heat it.
“We’ve put PV panels on the roof and the net gain from feed-in tariffs outweighs the amount of electricity and gas consumption. So, our net financial investment in energy is zero,” he said.
Though the couple love Ty Pren, Dave has notions of building another passive house — which would be his third self build. His limited budget at the outset of this project meant the plans for the house were actually adapted from an existing design Charles Gyrlls had drawn up, and he is toying with idea of building again — but this time starting with a blank sheet of paper, designing his dream home from scratch.
“There is a standard cliché that it takes three self builds to get exactly what you want,” he says. “I may never do it, it’s just a desire that I have.”
But he describes Ty Pren as “brilliant”— and is such a convert to the passive house standard that he has even helped persuade the local parish council to build their new community centre to the standard, too.
Selected project details
Clients: Dave & Claire Atkinson
Architect: Dempsey Decourcy Architects
Contractor: Mike Whitfield Construction
Passive house consultant: Elemental Solutions
Mechanical engineer: Alan Clarke
Structural engineer: Allan Pearce
Windows and thermal breaks: Green Building Store
Gas boiler: Worcester Bosch
MVHR: Paul, via Green Building Store
Airtightness products: Siga
Solar PV: Green Tech Renewables
Wind-tight membrane: Klober
Cellulose: Warmcel
-
Detailed cross section of the wall and foundation build-up Detailed cross section of the wall and foundation build-up
-
Erection of the timber frame superstructure on site Erection of the timber frame superstructure on site
-
Timber-frame I-beams resting on the edge of the slab, which helps to eliminate thermal bridging at the wall-to-floor junction Timber-frame I-beams resting on the edge of the slab, which helps to eliminate thermal bridging at the wall-to-floor junction
-
Timber I-beams at the wall-roof connection Timber I-beams at the wall-roof connection
-
Pump-filling the roof with Warmcel cellulose insulation Pump-filling the roof with Warmcel cellulose insulation
-
Klober Permo wind-tight membrane on installed on the roof of the house Klober Permo wind-tight membrane on installed on the roof of the house
-
Passive house consultant Nick Grant inspecting the installation of the windows, which are triple glazed and argon-filled timber units from Green Building Store Passive house consultant Nick Grant inspecting the installation of the windows, which are triple glazed and argon-filled timber units from Green Building Store
-
Paul Jennings of Aldas carrying out an airtightness test — the result of 0.16 air changes per hour is one of the best ever recorded in the UK Paul Jennings of Aldas carrying out an airtightness test — the result of 0.16 air changes per hour is one of the best ever recorded in the UK
-
Builder Mike Whitfield using smoke pencil to identify air leaks Builder Mike Whitfield using smoke pencil to identify air leaks
https://passivehouseplus.co.uk/magazine/new-build/the-west-midlands-eco-house-with-no-energy-bills#sigProId8862c5c2cd
1 Detailed cross section of the wall and foundation build-up; 2 erection of the timber frame superstructure on site; 3 timber-frame I-beams resting on the edge of the slab, which helps to eliminate thermal bridging at the wall-to-floor junction; 4 timber I-beams at the wall-roof connection; 5 pump-filling the roof with Warmcel cellulose insulation; 6 Klober Permo wind-tight membrane on installed on the roof of the house; 7 passive house consultant Nick Grant inspecting the installation of the windows, which are triple glazed and argon-filled timber units from Green Building Store; 8 Paul Jennings of Aldas carrying out an airtightness test — the result of 0.16 air changes per hour is one of the best ever recorded in the UK; 9 builder Mike Whitfield using smoke pencil to identify air leaks.
In detail
Building type: 140 (gross internal floor area) square metre detached two-storey timber frame house. Treated floor area 134 sqm. Plus workshop/garage.
Passive house certification: Not certified
Budget: £276,000 in total for all works. £200,404 for house only excluding outbuilding, landscaping etc (so £1,431 per sqm).
Space heating demand (PHPP): 9 kWh/m2/yr
Heat load (PHPP): 7 W/m2
Primary energy demand (PHPP): 83 kWh/m2/yr
Overheating (% time above 25C in PHPP): 1%
Heat loss form factor: 3.0
Airtightness (at 50 Pascals): 0.16 ACH
Energy performance certificate (EPC): C79
Energy bills: Approx £330 per year electricity bill & £350 year gas bill (total £680). However, Dave and Claire Atkinson receive approx £730 per year feed-in tariff for an estimated net energy profit of £50.
Thermal bridging: All thermal bridges modelled.
Ground floor: Flat structural slab on 250mm EPS insulation. U-value: 0.135 x 0.68 ground reduction factor = 0.092W/m2K
Walls: Douglas fir weatherboarding externally followed inside by 25mm counterbatten, Siga Majvest wind-tight membrane, 22mm wood fibre board, 350mm I-beams full-filled with Warmcel insulation, 18mm OSB, Siga Majpell vapour control membrane, 25mm counterbatten/service zone, 12.5mm plasterboard. U-value: 0.109 W/m2K
Roof: Reclaimed welsh slate externally, followed inside by 25mm batten, 25mm counterbatten, Klober Permo wind-tight membrane, 22mm wood fibre board, 400mm I-beam/full-filled Warmcel insulation, 18mm OSB, SIGA Majpell vapour control membrane, 12.5mm plasterboard. U-value: 0.091 W/m2K
Windows: Green Building Store Progression triple glazed, argon-filled, timber windows with ultra low maintenance Thermowood facing. Passive House Institute certified. Overall U-value: 0.68 W/m2K
Heating system: 95% efficient Worcester Bosch Greenstar 12i condensing gas boiler system (LPG) supplying minimal radiator system and single coil hot water cylinder. Hot water cylinder Worcester Bosch SC 180, total volume 190 litres. Solar PV supplied to the hot water immersion heater when there is surplus PV power, controlled by Immersun unit.
Ventilation: Paul Novus 300 heat recovery system with integral frost protection. Passive house certified heat recovery efficiency rate of 94.4 % at 145m3/h or 93% at 200m3/h.
Electricity: 14 sqm solar photovoltaic totalling 3.8kW Green materials: Recycled newspaper insulation, reclaimed slate, natural paints, locally sourced Douglas fir cladding, I-beams FSC-certified.
Image gallery
https://passivehouseplus.co.uk/magazine/new-build/the-west-midlands-eco-house-with-no-energy-bills#sigProId81efeed90c